Cnc Base For Prolight 1000
CNC 3020T-DJ/Mach3 - How To Setup And Operate Its Rotary Axis – A Complete Run - Duration: 12:36. Charlie Sarsfield 347,167 views. Super proLIGHT 1000 Ve r t i c a l M a c h i n i n g C e n t e r The newly engineered Super proLIGHT 1000 Standard Features Vibration-dampening polymer composite machine base Built-in chip tray.
These guys clearly have access to a REALLY nice shop to begin with which causes me to wonder at 3:25 of the first video why they milled the axis for the rails and the ball screw. As soon as I saw it I thought I’d probably have ground them. They appear to be doing the milling on a knee mill. While you can “swing” in the head (in another life I got really good at it with tons of practice) the bed still isn’t going to be able to churn out as precision results as would grinding. It would have taken a little more time, but saved them some of the headache of adjusting the rails if they ground a shoulder to register the location of the rails (which appear to be ground).
Still amazing to watch those guys work and as said before, Damn that is one beautiful clock. I have a ProLIGHT PLM2000. Intelitek discontinued the 2000 quite a while back but kept producing the PLM1000 and the enclosed Benchman version.
Both of those used stepper motors and Windows control software was written for them. The servo motor PLM2000 is stuck using the old DOS software.:( I finally managed to get someone at Moog Animatics to excavate some technical info and software from their archives for the 5000 series servo controllers which Light Machines used in the PLM2000. Posted on dropbox here Hopefully someone can use that to put support for the PLM2000 into modern CNC software like Linux CNC. Light Machines and Intelitek didn’t come near to fully utilizing the capabilities of the Animatics controller. What helps the ProLIGHT mills hold their value is they beat every new mill currently available in their size class on load capacity and speed. They can handle a 100 pound working load and the 2000 (dunno about the 1000) has traverse speeds up to 100 inches per second. To get something new with that kind of capability, it will cost a lot and will be larger.
5000, 1000 and 40K+ spindles were available, but the super high speed wasn’t an option on the 1000. If you’re looking to buy a PLM1000 mill, or PLT3000 lathe, make sure to get both the huge, black electronics box AND the ISA or (of course it’s better) PCI card plus all the connecting cables. If you do not get the interface card, you can buy one from Intelitek, at a price higher than what it’ll cost you to replace all the electronics with new stuff that runs with non-proprietary software. The PLM2000 is self-contained, all electronics in the ‘backpack’ box on the back of the column. Only requires 115VAC power and one RS232C connection to a control PC. Intelitek’s current small CNC machines are all (like most other companies still in the business) Sherline machines only good for doing tiny stuff.
Qurbani mp3 download. Light Machines built their mills and lathes with the capability to be used in light industrial, laboratory and educational fields – with the education not just on the basics of CNC operation but for learning about designing decently large things to be made by CNC machines. With a Sherline CNC, students can learn about CNC but they can’t do much about verifying a designing for manufacturing project, unless it can be done as a (very small) scale model.
Bigger one, made with smaller tools: I met the guy quite a long time ago (he is dead now), very skilled (professional machinist) but he intend to build the mill with only a small hobby desktop mill (BF20) and lathe (9×20 kind). He succeed quite well as his mill was able to mill steel easily.
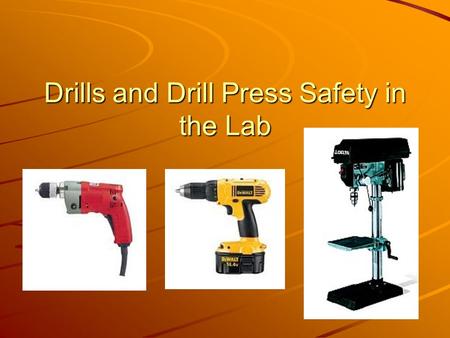
He has used clever way to overcome limited machining capacity: prepare mild steel rail support on the mill with notched design for supporting the rail, then finish with a hand scrapper and a machinist level (0.05mm/m sensitivity). The main limit with epoxy/granit is that you cannot make thin walled part like casting iron, minimum reliable size is around 50mm. Less than that and it can fracture under stress or deform. You also need big curing enclosure to maintain high curing temperature (depend on expoy used, but most high perf are high curing temperature), good mixer system. So it’s not a zero tool thing.